Scaling a hardware product from prototype to mass production, with 5 common pitfalls to avoid
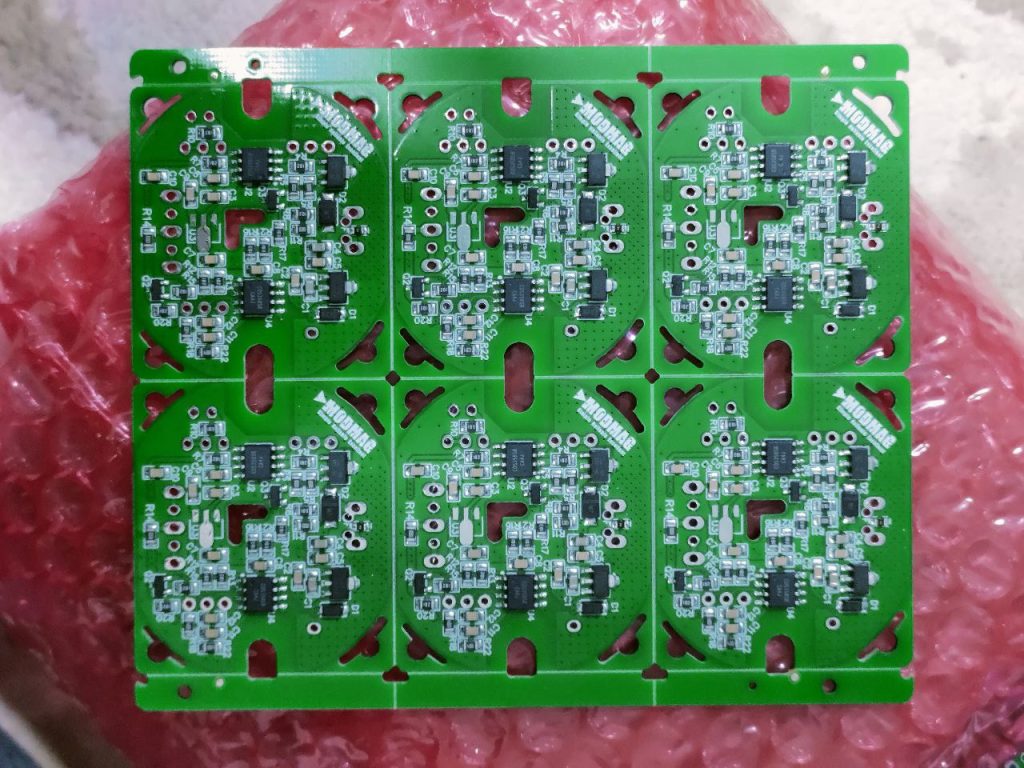
Introduction
Scaling a hardware product from prototype to mass production is one of the most critical—and challenging—phases for startups. Most hardware startups face delays in production due to unforeseen manufacturing issues. A design that works perfectly in the lab can fail spectacularly on the factory floor. This article explores the common challenges of scaling up and provides actionable strategies to ensure a smooth transition to mass production.
Table of Contents
Common Problems in Manufacturing and Scaling Up:
1. Yield Issues
Low yield rates—where a significant percentage of units fail quality checks—can derail production timelines and inflate costs. This often stems from design flaws, material inconsistencies, or assembly errors.
2. Supplier Inconsistencies
Variations in component quality or delays in delivery from suppliers can disrupt production schedules. Startups often struggle to manage multiple suppliers and ensure consistent quality.
3. Design for Manufacturability (DFM) Gaps
A prototype designed without considering mass production constraints can lead to costly redesigns. Issues like overly tight tolerances, complex assembly processes, or incompatible materials are common issues.
4. Lack of Manufacturing Expertise
Many startups lack the experience to navigate the complexities of mass production, such as selecting the right manufacturing process, optimizing assembly lines, or managing factory relationships.
5. Regulatory and Compliance Hurdles
Products must meet industry standards and certifications, which can be time-consuming and expensive. Non-compliance can result in costly recalls or legal issues.
Solutions for Smooth Scaling and Manufacturing:
1. Conduct a Design for Manufacturability (DFM) Review
Before moving to production, thoroughly review your design with manufacturing in mind. Key considerations include:
- Simplify Assembly: Reduce the number of parts and assembly steps to minimize errors.
- Optimize Tolerances: Ensure parts can be consistently produced within acceptable limits.
- Material Selection: Choose materials that are readily available and easy to work with.
- Test for Scalability: Validate that your design can be replicated consistently at scale.
Simplifying your product design and standardizing components reduced assembly errors and reworks.
2. Partner with Experienced Manufacturers
Collaborate with manufacturers who have expertise in your product category. They can provide valuable insights into process optimization, quality control, and cost reduction.
3. Implement Robust Quality Control Processes
Quality control is critical to maintaining high yield rates and ensuring customer satisfaction. Steps include:
- Incoming Inspection: Check components from suppliers for consistency and quality.
- In-Process Testing: Monitor quality at each stage of production.
- Final Inspection: Conduct thorough testing before products leave the factory.
Implementing automated testing systems, reducing defect rates, and increasing yield rates.
4. Build a Resilient Supply Chain
Diversify your supplier base and establish strong relationships with key partners. Strategies include:
- Dual Sourcing: Have multiple suppliers for critical components to mitigate risks.
- Buffer Stock: Maintain safety stock for high-risk components.
- Supplier Audits: Regularly assess supplier performance and quality.
5. Leverage Hardware Consultants
Hardware consultants bring expertise in scaling production and mitigating risks. They can help with:
- Process Optimization: Streamline manufacturing processes for efficiency.
- Factory Selection: Identify the right manufacturing partner for your product.
- Risk Mitigation: Anticipate and address potential issues before they arise.
6. Plan for Regulatory Compliance Early
Ensure your product meets all relevant industry standards and certifications. Steps include:
- Research Requirements: Identify the certifications needed for your market.
- Engage Testing Labs: Work with accredited labs to conduct compliance testing.
- Document Everything: Maintain detailed records for audits and inspections.
7. Start Small and Scale Gradually
Begin with a pilot production run to identify and resolve issues before committing to full-scale production. This approach minimizes risks and allows for iterative improvements.
Example: Conducted a pilot run of 100-500 units, to uncover and fix assembly issues before scaling to 10,000 units.
Conclusion
Scaling up from prototype to mass production is a complex but manageable process with the right strategies in place. By addressing manufacturability early, partnering with experienced manufacturers, and implementing robust quality control, startups can avoid common pitfalls and ensure a smooth transition to production.
Remember, the goal is not just to manufacture a product, but to do so efficiently, consistently, and at scale. With careful planning and the right partners, you can turn your hardware vision into a production-ready design.
Are you ready to take your hardware product from prototype to mass production with confidence? At MODMAG Egypt, we specialize in helping startups navigate the complexities of manufacturing and scaling. Our team of experienced hardware consultants will work with you to optimize your design, streamline production, and mitigate risks—ensuring a smooth and successful launch.
Don’t let manufacturing challenges slow you down. Contact us today to schedule a Free consultation and discover how we can help you scale faster, smarter, and more efficiently.